What is Six Sigma?
Quality management systems are generally designed to measure and improve quality. The goal of quality management is to produce a product that meets the expectations and needs of customers. Managing quality generally helps a business to reduce production defects, increase profits, and improves operational efficiency. Six Sigma is a quality-improvement program that aims to achieve a zero-level of defects in products and processes (Russell & Taylor, 2017). This statistical methodology is also used to improve business process and increase customer satisfaction. In statistics a sigma represents one standard deviation from the mean of a normal distribution. In statistical mathematics a Sigma is commonly represented by the Greek letter for sigma, which is σ, where the square root of σ is the variance of a set of data. Three σ or three-sigma in statistics refers to the probability of discovering some type of data point to be within a given range of 99.7%. Thus, considering the name of Six Sigma, it might be reasonable to surmise that probability of discovering some type of data point of a process to be within six-sigma, which truly could not be random chance from a statistical standpoint. The main idea of Six Sigma is that a process that can be measured can be improved. Six Sigma reduces the possibility of variations by using statistics to measure the standard deviation of a process and working towards keeping all processes in control. The goal of this process can be calculated based on the numerical goal of “3.4 defects per million opportunities, which is abbreviated as DPMO” (Russell & Taylor, 2017). This would be viewed as almost no defects from a statistical standpoint with all processes being in control. Having less defects in a process benefits companies in several ways. Some of these benefits include time savings, less expenses, and higher profit margins. If a product is defective it will take more time and money to fix or replace, which will reduce profit margins. Thus, a company can theoretically reach maximum levels of productional effectiveness when variations and defects are reduced to nearly zero.
About the Concepts
The concept of Six Sigma was originally founded on the premise of Dr. Deming’s Wheel of plan, do, check, and act, which is sometimes referred to as the PDCA cycle (Russell & Taylor, 2017). Since the creation of the PDCA cycle, the system has been modified many times to fit many different quality management systems. Motorola is credited as being the first company to implement the Six Sigma strategy (Six Sigma, 2013). The strategy helped Motorola to drastically improve quality and boosted profit margins. Companies from all types of industries and geographic locations soon after utilized the same strategy with lucrative results. Since the formation of the system many other companies soon after adopted a similar method with the hopes to achieve comparable results. As originally espoused by Motorola, Six Sigma utilizes the four basic steps of alignment, mobilization, acceleration, and governance (Russell & Taylor, 2017). Each of these steps have since been formalized into a structured process and a system for managing quality. There have also been additional steps and checkpoints added to help achieve the most ideal results.
DMAIC Process
The first step involves aligning top-level executives on the organization’s strategic initiatives and what improvement projects will have the greatest impact on the bottom line. A project Champion is then selected to be the process owner to supervise the improvement process (Russell & Taylor, 2017). The Champion is the top-level leader who oversees the improvement process and is responsible for utilizing Six Sigma principles in an improvement project. The Champion is sort of like the coach of a sports team because they provide leadership, guidance, and training when necessary. Mobilization empowers project teams to act to achieve zero defect (Russell & Taylor, 2017). During this step a team actively works to improve a quality issue that has been identified. Any issues in corrective actions taken during the improvement process would likely be discovered at this point and present an opportunity to correct it. Correcting any improvement efforts at this phase could help the project to stay on track. Six Sigma’s process for achieving zero defects through incremental improvement is based on the five steps called DMAIC. DMAIC stands for define, measure, analyze, improve and control (Six Sigma, 2019). Each step in the DMAIC process is listed in order. For instance, the problem must first be defined then measured and so on. These steps have since become the foundation for any Six Sigma project because of its ability and universality to solve problems.
DMADV Process
Six Sigma alternatively uses another five-step process called DMADV when more than an incremental improvement is needed in a process or when a completely new process is needed. DMADV stands for define, measure, analyze, design and verify (iSixSigma, 2019). Comparing the DMADV and DMAIC process it is noticeable that the first three steps in the process are the same. This means that regardless of the improvement project, both methodologies require the issue to be defined, measured, and analyzed. The difference in these two methods are the last two steps of the method. DMADV is also known as Design for Six Sigma or DFSS, which is used for developing new processes or a product (Russell & Taylor, 2017). Both sub-methodologies stem from a step zero, which is based on employees being trained in Six Sigma Leadership. The Champion of a project chooses Six Sigma trained Black Belts to lead their team based on a DMAIC or DMADV problem-solving method. Acceleration is the third step in the Six Sigma process that involves trained Black Belts and Green Belts with suitable expertise to implement an action-learning tactic to increase the team’s capacity to execute the project more effectively (Russell & Taylor, 2017). The concept of acceleration requires implementing more Six Sigma trained team members that have relevant experience to help fast-track improvements and increase project efficiency. In some cases, this step involves additional training, education, and coaching. Continuous review and reporting to the project champion will ensure that project actions can meet an aggressive timeline. The forth and final step of the Six Sigma process involves governance. Governance involves the executive process owners regularly reviewing project reports to make sure the improvement projects are progressing as anticipated (Russell & Taylor, 2017). During this step the process owners share information about all ongoing improvement projects to combine and compare findings to maximize the benefits of project efforts. All four of the Six Sigma process steps are aimed to address a need to improve quality and increase overall customer satisfaction.
About the Six Sigma Hierarchy
A Six Sigma project utilizes a hierarchy of various degrees of certification and training to achieve optimal results. Master Black Belts oversee processes executed by both Black Belts and Green Belts (iSixSigma, 2019). They also provide support and instruction to Black Belts and Green Belts. The hierarchy of Six Sigma is very similar to any corporate structure with multiple levels of positions and roles. The main difference is that someone who is highly trained in Six Sigma has more formal training on the general methodologies of the system and relevant experience. The idea is that a Master Black Belt has a lot of experience in utilizing Six Sigma and can provide their expertise to Black Belts and Green Belts that have less experience. In a corporation this would be like the executives giving directions to the directors, directors to managers, and so on.
A person must be well-trained in statistical methodologies and have successfully completed about twenty different Six Sigma projects to obtain Master Black Belt certification (Russell & Taylor, 2017). The main difference between Black Belts and Green Belts is there level of certification and project experience. Black Belts are extensively trained in statistical methodologies and their main line of work must involve over seventy-five percent of their time at work being dedicated to completing four to six-month Six Sigma projects (Six Sigma, 2019). Black Belts have less experience than Master Black Belts but are the second most experienced and trained in Six Sigma. Green Belts are also trained in statistical methodologies and at least fifty percent of their time at work must be dedicated to completing four to six-month Six Sigma projects (Six Sigma, 2019). Having employees who are highly trained in Six Sigma certifications helps to ensure projects can effectively and efficiently reduce variations and improve quality. People trained in Six Sigma have relevant experience and advanced statistical models to more quickly and accurately identify opportunities for improvement.
People that are trained and certified in Six Sigma utilize tools and statistical measurements to improve business processes and capabilities. These increases in operational performance and decreases in the variation of processes leads to reducing defects, profit improvements, boosts in employee morale, and increases in the overall quality of products and services (American Society for Quality, 2019b). A person well-trained in Six Sigma could use statistical measurements to help a company to identify an issue in manufacturing that causes defects, as well as, accurately calculate how much those defects take away from profits. For example, a widget company may find that for every one-hundred widgets produced that three to five of those widgets are defective. A person trained in these systems would be able to identify the statistical probability of such defects and accurately determine how much those defects cost the company beyond the obvious cost of the product. These costs could be calculated based on the time it takes to reproduce a new widget, the man power required, the time it takes to check quality of the product and so on. The tools utilized by Six Sigma trained experts involves utilizing qualitative and quantitative techniques to improve processes. Being trained in Six Sigma tools also requires being proficient in statistical methodologies, which includes Quality Function Deployment (QFD), Cause and Effect (C&E) Matrix, Failure Modes and Effects Analysis (FMEA), t-Tests, Statistical Process Control (SPC) charts, and Design of Experiments (DOE) (Russell & Taylor, 2017). These are just a few of the tools that Six Sigma utilizes to improve business processes. The emphasis of these Six Sigma tools is to determine standard deviations from a process mean with a chief aim to reduce defects and eliminate variations.
References
American Society for Quality (2019a). W. Edwards Deming. Retrieved from https://asq.org/about-asq/honorary-members/deming
American Society for Quality (2019b). What is six sigma? Retrieved from https://asq.org/quality-resources/six-sigma
American Society for Quality (2019c). W. Edward Deming’s 14 points. Retrieved from https://asq.org/quality-resources/total-quality-management/deming-points
Culture of Life Studies Program (n.d.) John F. Kennedy. Retrieved from https://cultureoflifestudies.com/resources/one-person-can-make-a-difference-and-everyoneshould-try-president-john-f-kennedy/
Hoyer, R. & Hoyer, B. (2001). What is quality? American Society for Quality. Retrieved from http://asq.org/qic/display-item/index.html?item=14959
iSixSigma (2019). What is six sigma? Retrieved from https://www.isixsigma.com/new-to-six-sigma/what-six-sigma/
Kaizen Institute (2014). Deming’s 14 principles. Retrieved from https://kaizeninstituteindia.wordpress.com/2014/08/04/demings-14-principles/
Lean Production (2019). Kaizen. Retrieved from https://www.leanproduction.com/kaizen.html
Russel, R. & Taylor B. (2017). Operations and supply chain (9th ed.). Danvers, MA: John Wiley & Sons, Inc. Retrieved from https://purdueuniversityglobal.vitalsource.com/#/books/9781119320975/cfi/6/18!/4/2/2/2/2@0:0
Six Sigma (2019). Welcome to 6sigma.us. Six Sigma. Retrieved from https://www.6sigma.us/six-sigma.php
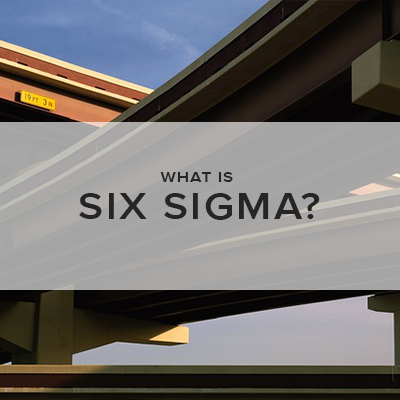
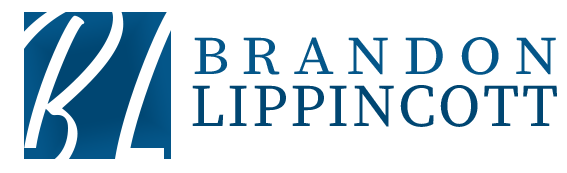